From Gantt to Flowlines / Locationbased Scheduling
Take a minute to look at the colored diagonal lines (activities) in the figure at the bottom picture in the illustration below (Ca, Br, Pa,El).
When they are copied from the top schedule (Gantt) down to the bottom schedule (location-based), you can see what happens when these lines/activities are divided into locations:
– 2nd floor
– 1st floor
– Ground floor
When the lines (activities) are split into locations – they change to the characteristic diagonal lines – also known as flowlines. Theseflowlines hold information about activity, time, and location.
Now,buckle up; let’s get started and find the five fatal flaws.
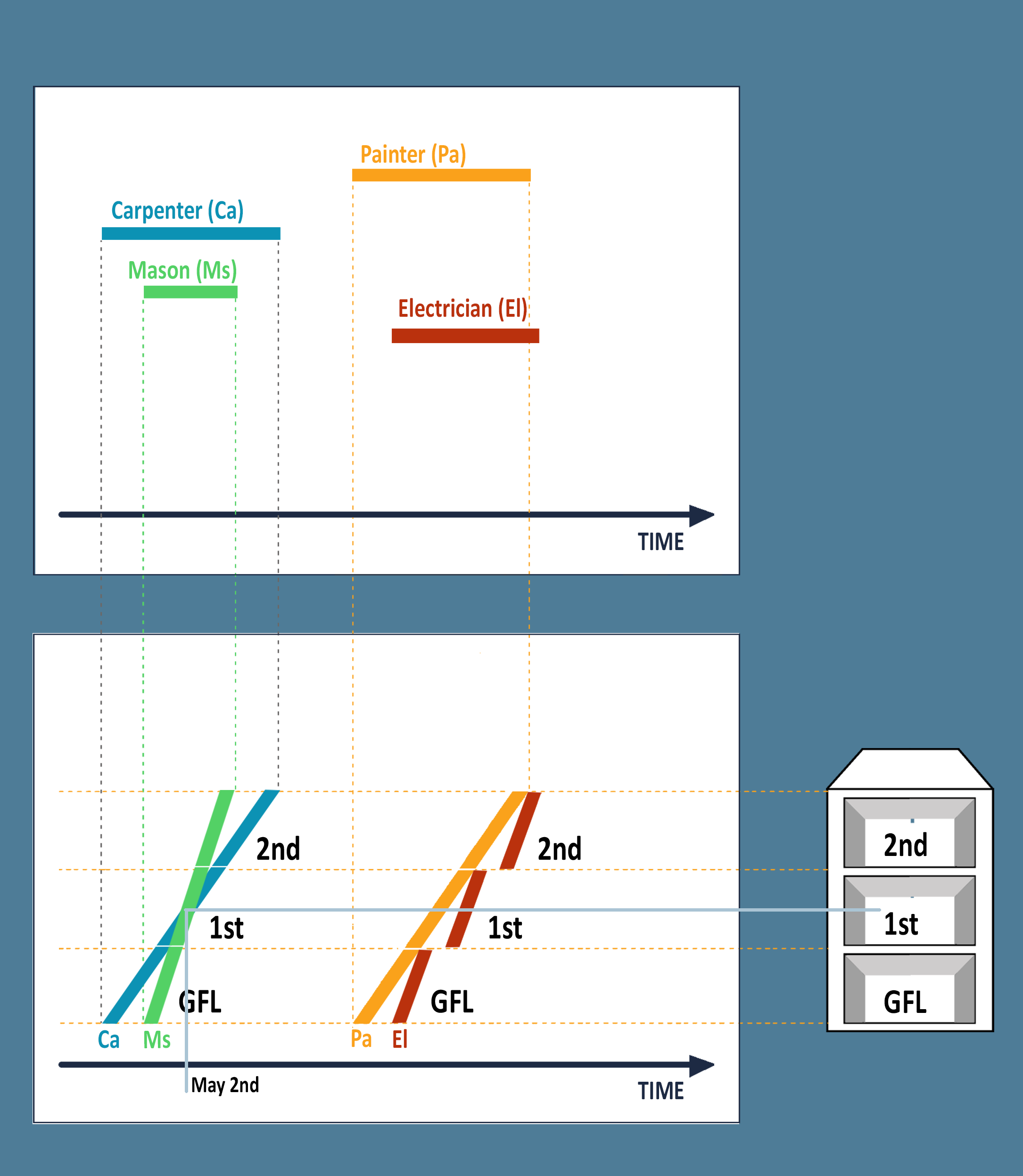
Flaw no. 1 – Colliding Activities
The first flaw is colliding activities.
In the flowline view, these collisions become visible where two flowlines intersect – indicating that multiple trades are scheduled to work in the same location at the same time.
Depending on the activities, this may or may not be a problem. For example, a carpenter can install kitchen cabinets while a mason tiles the bathroom – no conflict there. But if the carpenter is behind schedule and the bathroom walls haven’t been built yet, the mason can't begin.
In such cases, overlapping work causes delays and wasted time.
This type of uncoordinated scheduling often leads to contractors standing idle, which costs them money and strains collaboration. A “first come, first served” mindset can develop on-site, fueling daily frustration and undermining team spirit.
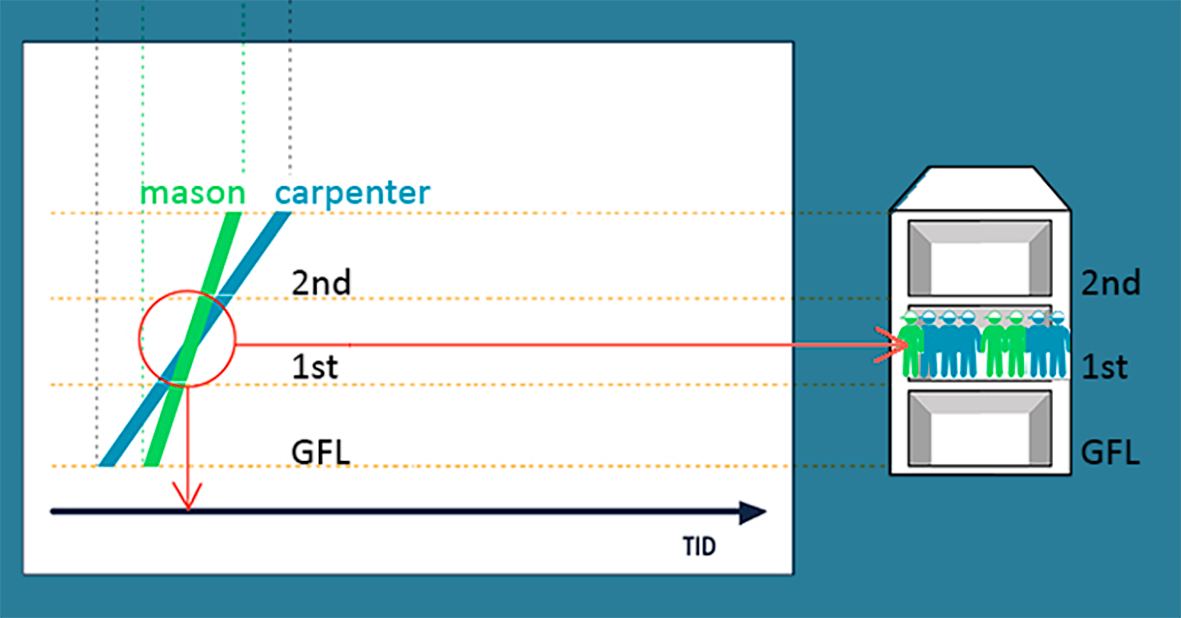
Flaw no. 2 – Empty Locations
What this means in everyday life on the construction site is that some areas remain completely unused – while others are over crowded and chaotic.
Ina line-of-balance (location-based) schedule, these idle areas are significant gaps between the diagonal flowlines – a clear sign that no work is planned in those locations.
When the schedule is based only on time and activities – without considering location – both Flaw No. 1 (collisions) and Flaw No. 2 (empty zones) appear.
The result is a random distribution of work: Some trades crowd into the same space, while others drift to wherever there's room. Contractors end up working in locations that happen to be available that day – not because it was planned.
This randomness creates an inconsistent,stop-and-go workflow, adds waiting time, and impacts the contractors’ earnings.And just as importantly – it puts a strain on teamwork and the overall tone onsite.
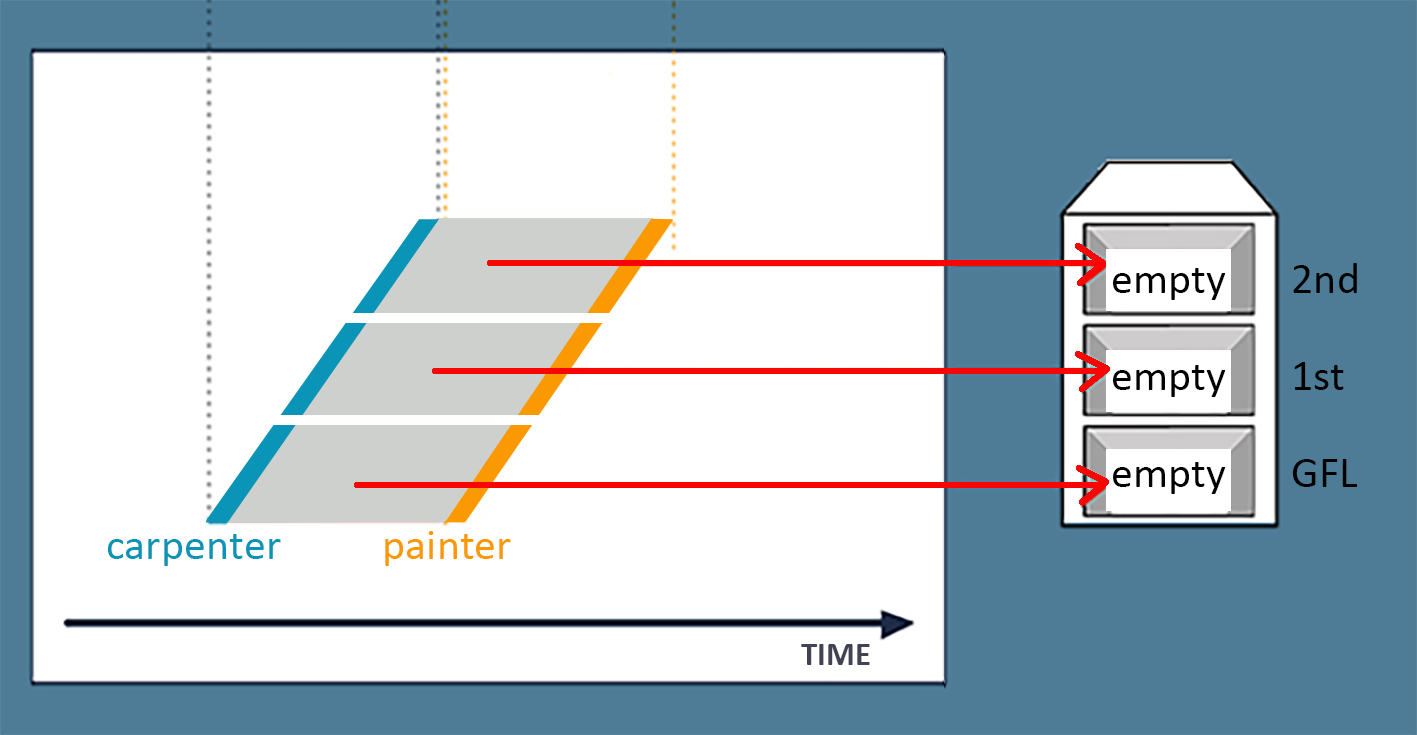
Flaw no. 3 – Wasted Time from Start-and-Stop Work
Waiting time is one of the most critical factors affecting contractors’ productivity and earnings.
These interruptions are visualized by broken lines in a flowline schedule – a clear indicator of a stop-and-go workflow. As shown in the illustration, the painters (orange) must either speed up or the electricians (red) must slow down to create a smoother handoff between trades.
Waiting times become just as random when activities are scheduled at random locations without considering dependencies. This is especially problematic when there are dependencies between trades.
For example, a mason can’t start tiling until the carpenter has finished building the bathroom wall.
The result? The masons are left waiting and cannot access the location until the carpenters are done. This kind of imbalance causes avoidable delays, inefficiencies, and frustration on site.
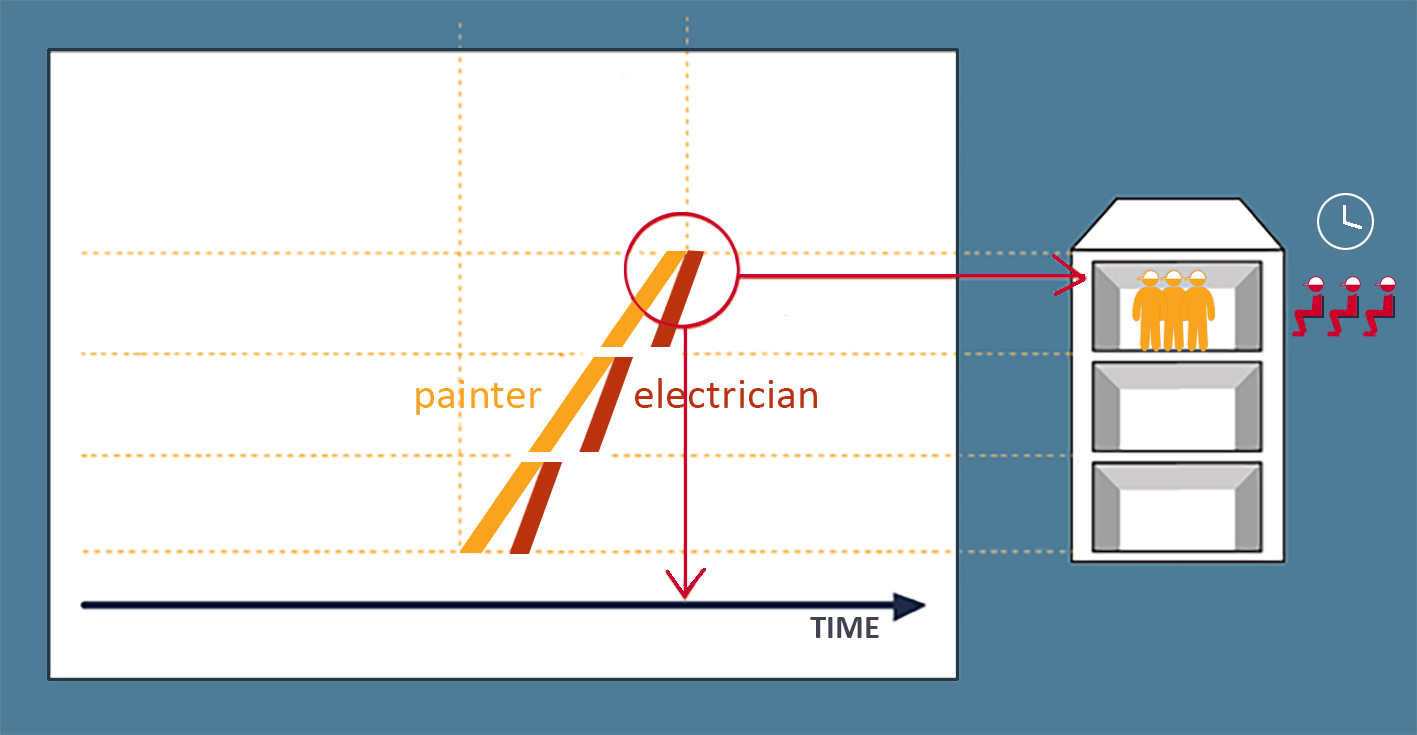
Illustration: To resolve the issue in this graphic example, the electrical team has to find more men for the crew to work faster, or the painter has to redirect some men to another location on-site to “work slower.”
This will ensure a good workflow between the two disciplines.
Flaw no. 4 – Uneven Staffing and Disrupted Flow
Random deployment of teams on-site is one of the main causes of inconsistency – which often leads to delays on-site.
The ideal scenario is a steady, uninterrupted flow of work: Aconsistent number of teams from each trade, moving from "location 1"to "location 100" – without stops, gaps, or overlaps.
The result is chaotic, when focusing on consistent staffing isn't part of the planning process. Take this example: Due to poor planning, six carpenter teams showed up on site one day – with only work for three. Half of them were sent to another project nearby, wasting time and energy.
Without structured resource planning, teams float in and out at random – trying to get something done before being pulled off the job again.
This instability disrupts progress, damages morale, and contributes to a poor working environment – not just on one site but every site involved.
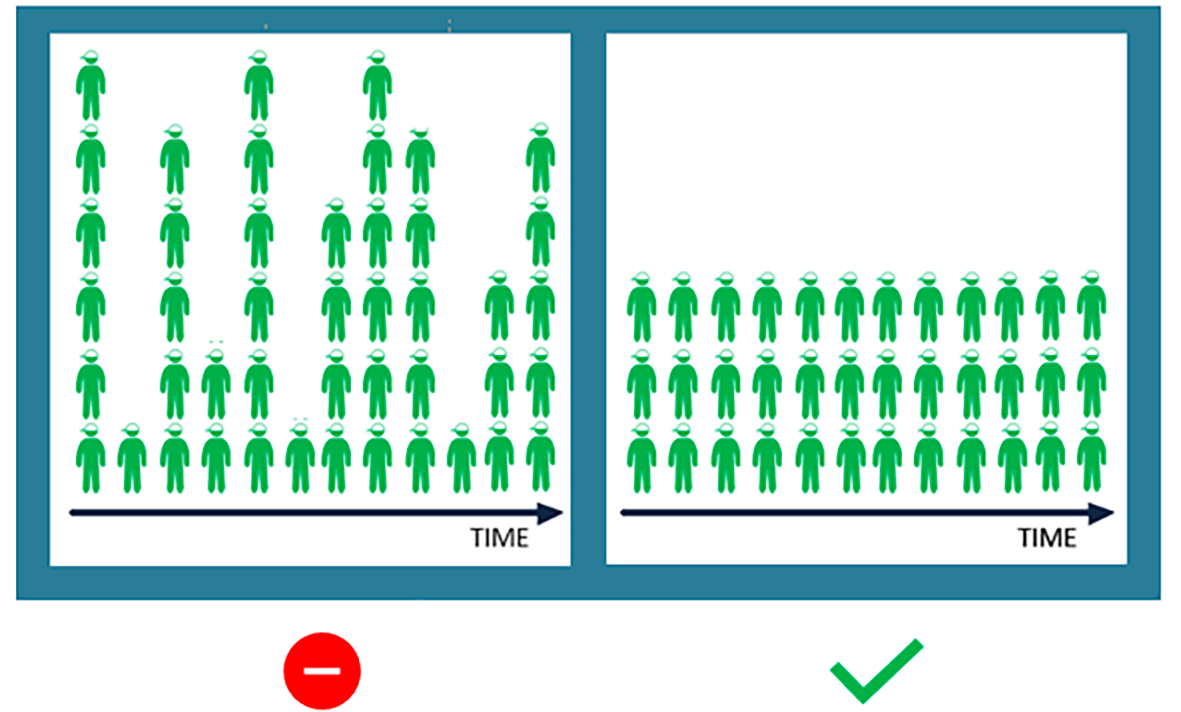
Flaw no. 5 – No Visibility Into the Consequences of Delays
Once construction begins, delays are inevitable. Unexpected events will always occur in construction. No way around it. And it will always affect the schedule.
However, with a Gantt chart, it's nearly impossible to see how a delay in one location or by one team affects the rest of the project.
With a line-of-balance (flowline) schedule, on the other hand, you can forecast and visualize the consequences of delays and changes. You can see how they impact specific teams, trades, locations, resource allocation, dependencies – and the overall deadline.
It also allows you to challenge unrealistic optimism and “wishful thinking” at weekly site meetings. - In this example the carpenter is behind schedule:
“Sure,we are a bit behind, but don't worry, we'll still hit the deadline.” (!)
With flowlines, you canvisualize whyhis wishful thinking is not realistic. You can show him exactly how his delay will affect the following trades and why the project's end date is now at risk.
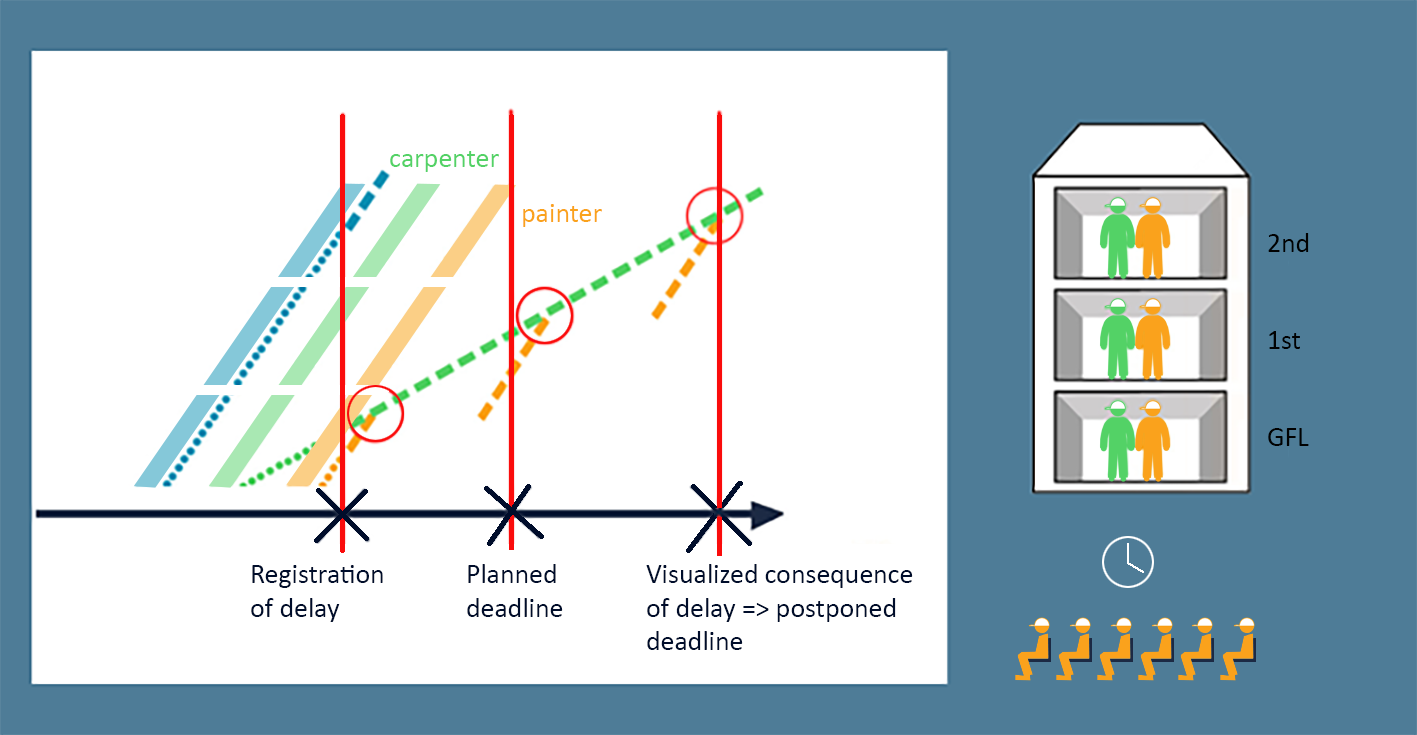
Illustration: The heavy green line illustrates the carpenter's planned work. The green dotted line illustrates the carpenter's actual pace. If the carpenter doesn't bring more workers on-site, the dotted line will follow its new path, resulting in waiting time for the painters and a delayed deadline.
No more guesswork and wishful thinking; facts are visualized. With flowlines you have time to act before things spiral out of control.
Adjust in time!
However, if the carpenter does bring more workers on-site in time, it is possible to redirect and adjust the “new (slow) path” and meet the deadline!
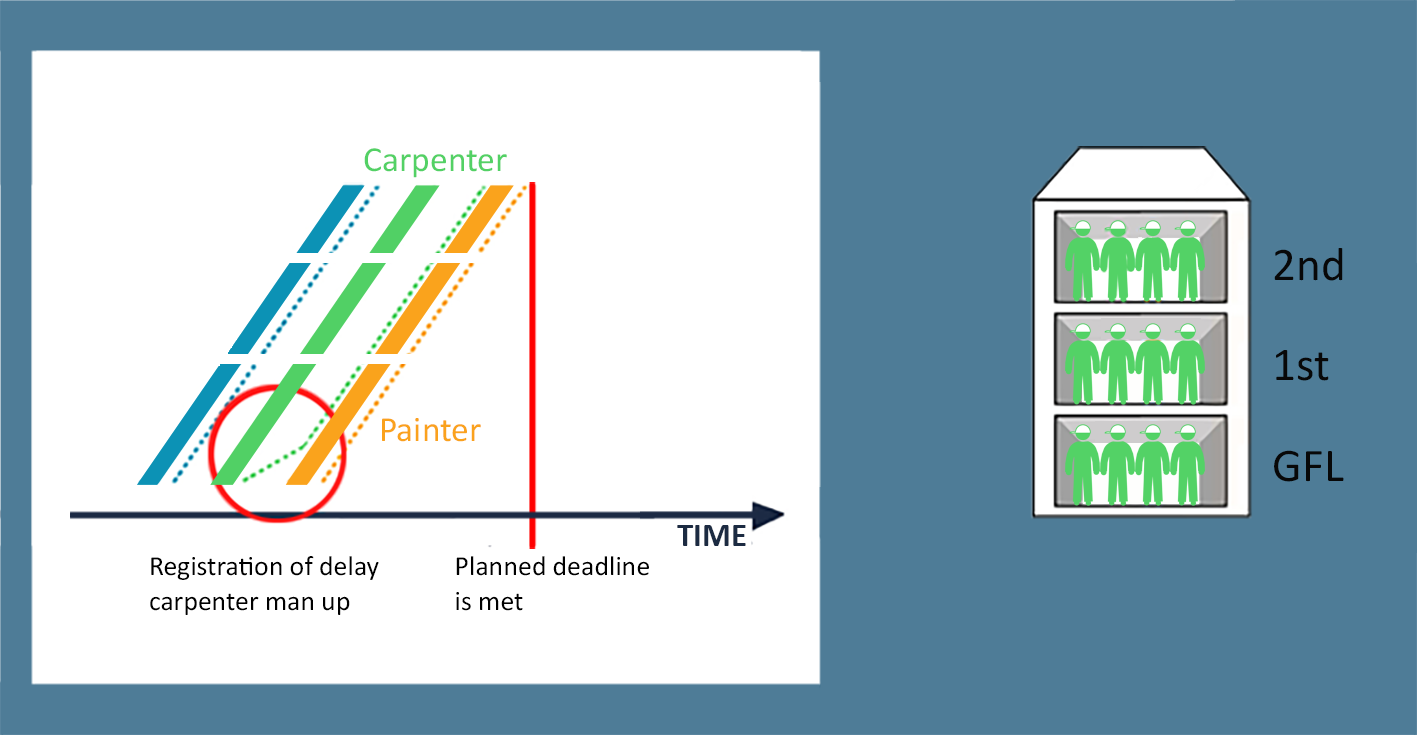
Interested in learning more?
Reach out to Kristina at info@tactplan.com – she’ll help you get started.
We’re happy to offer you a free personal web introduction to location-based scheduling and our construction scheduling and construction management software. You’re also welcome to explore Tactplan with a free trial.